How does ERP Software help Improve Order Fulfillment in Your Warehouse?
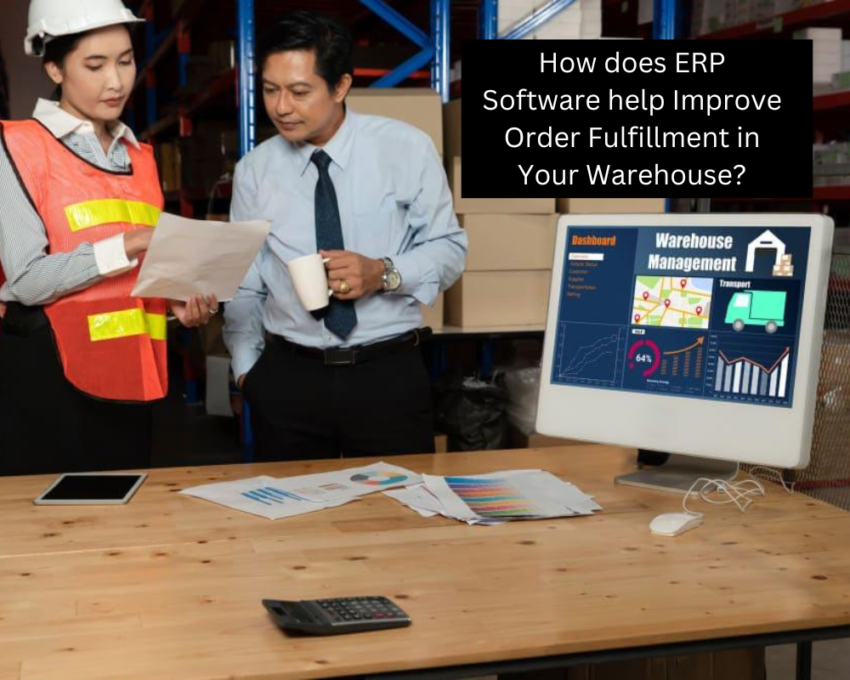
Processing orders is an important aspect of the business. The main purpose of order fulfillment is to deliver the order safely to the customers on time, container yards, or warehouses quickly to retain and balance customer loyalty. The consequence of good order fulfillment processes will help in gaining repeat customers which will be valuable for the business. Plus, it attracts many new customers. ERP system is an efficient solution to manage the entire order fulfillment process without any hassle.
What is the Order Fulfillment Process?
It is an achievement for businesses when they get ample sales. However, the real celebration can be done only when the customer receives the order in their hands. Order processing involves the process of assembling the order and shipping it off to the customer. Further, adequate support is also provided to the customer.
The order fulfillment process is a major five-step process and it begins with the sourcing of the product and ends with the shipping of the same. For many businesses, order fulfillment encompasses inventory management, supply chain management, order processing, quality control and customer support.
Depending on the size of the business, the order fulfillment process can happen under a single roof if the warehouse is well organized. The entire process is done in a single place mostly by small businesses. As far as large-scale organizations are concerned, they require a more complex strategy such as a multi-layer distribution center strategy. Whatever the strategy is, the objective of this process is to deliver customers’ orders quickly, reliably and inexpensively.
How does the Order Fulfillment Process work?
We learned earlier that the order fulfillment process involves operations such as inventory management, supply chain management, order fulfillment, quality management and delivery support for the customers( regarding reporting issues, product exchange or returns). The five steps of the order fulfillment process are listed below.
- Incoming goods source – Manufacturers, farms, wholesalers.
- Receiving orders – Distribution centers
- Storage – Products kept for a short term.
- Processing – Involves picking up and packing products.
- Shipping – Transporting orders to the customer
1. Receiving Inventory
Here the goods are received from a third party or from another department in the company or from a company warehouse. It can also be received from the pipeline and is applicable to products such as water, oil, fuel or any other fluid. The receiving inventory can also be digital data from a database or in other distinct forms from internal or external sources.
2. Inventory storage
The received goods are then sent to a short or long-term storage center. The goods are stored till the distribution centers are organized. First, the existing sales are completed and then the stored goods are sold.
3. Order Processing
As the orders are received from the customers, the order fulfillment process facilitates the picking up and the packing up tasks. So, if it is an online marketplace, integrating order management software with a shopping cart of the e-commerce site will be helpful for simpler order initiation.
4. Picking
After the order is initiated, a picking team or automated robots select items from the warehouse based on the information specified in the packing slip. The slip contains information such as the list of item SKUs, sizes, product colors, number of units and its location in the warehouse.
5. Packing
The packing team selects the packing materials or using automated fulfillment robots will help in obtaining the lowest dimensional weight which is calculated by multiplying package length times and width times height. Optimizing dimensional weight is vital as space on the truck is premium and also it will reduce the shipment costs.
In addition, the packing process also involves returning shipping materials, in case the customer returns the order.
6. Shipping
The order is then sent to shippers and carriers such as freight services, trains, airlines etc. It determines the freight billable costs based on the dimensions and the weight of the package. Even if the packaging weight is low, the lowest DIM is documented for the product if it is T-shirts etc. If the space and weight are not done properly, then the shipment delivery will be delayed more.
7. Delivery
More than one carrier can be included for the shipping routes. Even in the remote areas, the goods are delivered using two carriers. For example, one carrier picks from the delivery center and the other carrier further delivers the product to the customer.
8. Returns
In this stage, the return material is attached to the customer’s returned product. A label, packaging materials etc. are included with the product. The product is then safely sent to the warehouse where it is restocked again. Later, it is returned to the manufacturer, distributor, or vendor and then a refund is initiated.
Read: How does Azure consulting services boost your business performance?
Importance of Order Fulfillment
The significance of the entire order fulfillment process is that businesses make money by selling goods, products and services directly to the consumers. The company may be B2B or D2C, the sale is considered complete only when the product is delivered to the customer. Order fulfillment is of paramount value as it reveals a company’s ability to conduct sales.
ERP Software features to improve Order Fulfillment in the Warehouse
Enterprise resource planning software is an expert in managing all the activities of the business. It has rich features which will proficiently assist the order fulfillment process.
1. Freight software
The advanced feature to manage multi-carrier services where it connects shipping with order entry, accounts receivable and customer services. All these factors help in streamlining the order fulfillment process.
2. Inventory Forecasting software
The historical data stored in the software can be accessed to comprehend when to order and the total amount to order.
3. Replenishment software
It provides features to help reduce waste and increase inventory turnover. In addition, it maintains an efficient order and line item fill rate.
4. Buying history analytics
The history of the customer purchases can be accessed. Plus, it helps in receiving alerts regarding any irregularities happening in the account.
Conclusion
ERP solution is the best software to sort out all the processes of order fulfillment. It can complete all the stages of the order fulfillment process efficiently. Business owners, managers and the order fulfillment team can access the system for information in real-time. The product can be tracked from anywhere in the world seamlessly.
Author’s Bio:
Sneha Rakte is a specialist in communication who excels at recognizing client requirements. She produces persuasive sales copy and high-converting content. She currently works with Sage Software Solutions, an industry leader in supplying small and medium-sized enterprises in India with high-quality ERP software and CRM solutions.