Driving Efficiency in Industrial Machinery Maintenance
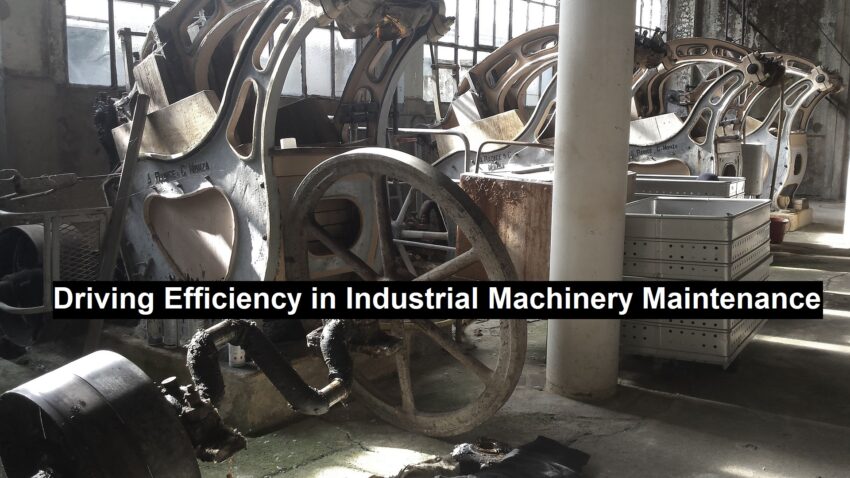
Maintenance costs in industrial settings can be substantial, impacting both time and capital. To maintain a competitive advantage and maximize ROI, businesses must adopt effective maintenance strategies. The global MRO market is projected to reach $701.3 billion by 2026, underscoring the need for cost-effective solutions.
Unplanned downtime, caused by aging equipment and mechanical failure, is one of the largest contributors to these costs. To mitigate downtime, industries are adopting low-maintenance technologies such as ultrasonic clamp-on meters. These components eliminate the need for regular servicing, helping to reduce long-term maintenance costs.
Read: Boosting Phone Performance: The Importance of Digital Decluttering
Preventive maintenance (PM) is another widely used method. In 2020, 76% of manufacturers implemented PM to identify potential problems before they lead to downtime. While this approach increases the cost of ownership, it helps extend the life of equipment and minimizes operational disruptions.
Predictive maintenance (PdM), an emerging technology, offers further cost-saving opportunities. Using sensors and AI, PdM can monitor equipment in real-time to predict when repairs are necessary. Currently adopted by 41% of manufacturers, PdM can save up to 12% in maintenance costs compared to traditional methods.
Driving-Efficiency-in-IndustrialBy embracing these advanced maintenance strategies, businesses can improve operational efficiency, reduce downtime, and lower overall costs. For more information on how these advanced strategies are improving organizational output, please see the infographic provided by Emerson.